Gravity die casting process pdf
way to realize the water jacket in the high-pressure-die-casting process with a permanent and retractable steel-core. The weaker structure may lead to higher bore distortions and it
The die casting die or mold is a closed vessel into which molten metal is injected under high pressure and temperature, then rapidly cooled until the solidified …
This paper deals with elimination of defects in aluminium alloy castings produced by gravity die casting process. The main intention of work is to investigate the defects and improve quality of a gravity die cast component using Computer Aided Casting Simulation Software. In this study an industrial gravity casting die is used which was producing defective components. The die and components
the low pressure die casting process. During solidification simulation, the evolution of the solid fraction is calculated and used to predict shrinkage locations. Air back pressure calculations together with appropriate user-defined pressure conditions allow the simulation of vacuum casting processes. High Pressure Die Casting ESI’s QuikCAST allows you to perfectly simulate the piston
Gravity die casting of AC4C aluminum alloy with mechanical vibration (0–120Hz) was conducted. Columnar rod specimens Columnar rod specimens ( 25mm L210mm) were cast to investigate the effect of mechanical vibration on the cooling rate and the dendrite arm spacing of AC4C
The gravity die casting process is suitable for high volume production of non-ferrous alloy castings of Aluminium, Magnesium, Copper and Zinc base alloys and to limited extent for cast iron castings. Castings can be manufactured by operation of dies manually or by automatic devices or through die casting machines depending on the quantum of production. The die materials used are gray cast iron
‘Aluminium Cylinder Head’ castings by Gravity Die Casting process. • Technical Assistance Agreement’ with WP Suspension (subsidiary of KTM). • Joint venture with Magneti Marelli Holdings S.p.A. for manufacture of four-wheeler suspension products in India II. L
7/04/2017 · In this video of Aluminium Gravity Die Castings where molten Aluminium/Metal is poured into a cast iron gravity die tool. The two hardened tool steel dies has created the cavity which work as
Gravity die casting allows for a more precise control over dimensional attributes than sand casting processes are able to. The casting process itself is highly …
Gravity Die Casting Gravity die casting is a process wherein the liquid metal is poured into metallic moulds without application of any external pressure. The liquid metal enters the cavity by gravity. Gravity die casting (GDC) is different from High Pressure Die Casting (HPDC), where the liquid metal is injected into the metal mould under very high pressures for production of thin walled
A PRACTICAL APPROACH TO ELIMINATE DEFECTS IN GRAVITY DIE
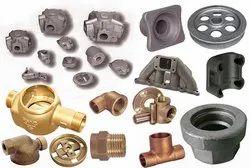
Gravity Die Casting Manufacturing Process/machine Castal
Casting Process Data Sheet. Input Data needed to run the simulation: Sand Casting-Casting Process Data Sheet.pdf. Low Pressure Die Casting-Casting Process Data Sheet.pdf
casting processes, such as permanent mold casting process) can be considered a “defect generating process”. Not only an average 5-10% scrap is typically produced, but the type, size and severity of defects are varying. From these considerations, it seems that the potential of high-pressure die-casting and permanent mold casting processes will be completely exploited only when the quality
Permanent mold casting is a process used in which permanent molds consists of mold cavities, machined into metal die blocks and appropriate for repetitive use. Advantages This type of casting process is less expensive than die casting or investment casting.
This process is also called counter-gravity casting. It is basically the same process as investment casting, It is basically the same process as investment casting, except for the step of …
ABSTRACT :Gravity die casting is used to manufacture the complex metal components where there is a need for high structural integrity. The casting defects that are caused by molten metal include air entrapment, porosity, and shrinkage. But the control of casting defects has been based on the experience of the foundry engineers. This paper describes these defects in casting with the help of
Gravity Die Casting employs cast iron or steel moulds which allow aluminium and zinc castings to be produced more accurately and cheaply than with sand casting, with better surface finish, and better mechanical properties.
Die casting is a process that has been around for several decades. It is a flexible process for producing metal It is a flexible process for producing metal parts by forcing molten metal under pressure into reusable steel molds or dies.

The gravity die casting process is governed by its process parameters so it is required to study its process parameters and its effects. In this paper an effort has been incorporated to study the change in process parameters and their consequent effects on casting defects. Key words:
MRT Castings is delighted to announce the purchase of a new PFO250 fully automated, die casting cell, from Italian manufacturer Colosio. Read More MRT are exhibiting at Southern Manufacturing & Electronics Exhibition 2019
The aluminium die casting process is used to create precise, uniform aluminium components. Lupton & Place are some of the most experienced manufacturers in the UK, using the die casting process to ensure a great result for our clients, every time. Learn more about the die casting process on this page or …

The die casting process has evolved from the original low-pressure injection method to techniques including high-pressure casting at forces exceeding 4500 pounds per square inch squeeze casting and semi-solid die casting. These modern processes are capable of producing high integrity, near-net-shape castings with excellent surface finishes.
Die casting is the process of forcing molten metal, under high pressure, into mold cavities (which are machined into dies). Most die castings are made from non-ferrous metals, specifically zinc, copper, aluminum, magnesium, lead, and tin based alloys, although ferrous metal die castings are possible. The die casting method is especially suited for applications where a large quantity of small
While vacuum die casting of aluminum is widely practiced, there is only one company in North America, Gibbs Die Casting (Henderson, KY), that uses vacuum for die casting magnesium components. Fig. 7 shows the Gibbs vacuum-assisted vertical die casting process [11] .
Posted on 17th November 2016 Pressure vs Gravity Die Casting. We’ve previously discussed the differences between forging and investment casting, so now we’re turning our attentions to how pressure and gravity die casting differ from each other – and which similarities they have in common.
Gravity Die Casting Description. Gravity die casting can also be referred to as chill casting or permanent mould casting. Gravity casting is the process of pouring molten metal into steel or cast iron moulds where there is no force other than gravity.
Gravity Die Castings Die casting products, mainly are cast aluminum alloy and zinc alloy with good dimensions. Lost Foam Castings Lost foam casting products, ductile iron pipe fittings, valves Low Pressure Die Castings Lost pressure die casting products, mainly aluminum alloy casting products.
Gravity die casting is an important casting process which has the capability of making complicated, high-integrity components for e.g. the automotive industry. In gravity die castings, the major
automatic machines as die-caster operator. 3. Employment opportunities: On successful completion of this course, the candidates shall be gainfully employed in the following industries: 1. Low Pressure die casting Industry. 2. High Pressure Die casting Industry. 3. Gravity Die casting Industry. 4. Further learning pathways: reputed Industries / Organizations. ssful completion of the course
Effective Die Coating for Maximum Value . In gravity diecasting, coatings can be used to present die wear and control metal solidification rate and direction
Die casting is a metal casting process in which molten metal is forced into a steel mold under high pressure into a mold cavity. The steel molds, known as dies, are fabricated to produce castings with
Gravity Die Casting Carlton Die Cast
We can produce gravity castings up to 1.5 x 1.2 metres. Shot weights range from 0.2 kilogrammes up to 45 kilogrammes, and we use six different aluminium alloy specifications. We manufacture a diverse range of castings including footplates, valve components, safety-critical suspension assemblies, housings and brackets.
Chapter III: Manufacturing Process & Technology 3.1 Sand casting 3.2 Die casting 3.2.1 Gravity die casting 3.2.2 High pressure die casting 3.2.3 Low pressure die casting 3.2.4 Basic difference between the 3 die casting processes 3.3 Squeeze casting 3.4 Aluminium casting alloys designation 3.4.1 Standards governing aluminium casting alloys 3.4.2 Aluminium casting alloys family and their end …
Die Casting. Gravity die castings are manufactured in aluminium and zinc up to a weight of 25 Kg. High pressure die castings are also manufactured in aluminium and zinc on machines ranging from 250 ton up to 725 ton. – gating system in sand casting pdf
Gravity Die Casting Casting (Metalworking) Alloy
Carlton Die Casting Gravity and High Pressure Die Casting
CASTING SIMULATION SUITE esi-group.com
STUDY OF PROCESS PARAMETERS OF GRAVITY DIE CASTING
CMH Articles
DIE CASTING AUTOMATION – AN INTEGRATED ENGINEERING
Aluminum gravity die casting PowerPoint PPT Presentation
https://en.m.wikipedia.org/wiki/Centrifugal_casting_(industrial)
Casting Data Sheet SUTCAST
fundamental forecasting of exchange rates example –
A PRACTICAL APPROACH TO ELIMINATE DEFECTS IN GRAVITY DIE
Linear Casting Tolerances Linear Dimensional Tolerances
Die casting is a process that has been around for several decades. It is a flexible process for producing metal It is a flexible process for producing metal parts by forcing molten metal under pressure into reusable steel molds or dies.
The die casting process has evolved from the original low-pressure injection method to techniques including high-pressure casting at forces exceeding 4500 pounds per square inch squeeze casting and semi-solid die casting. These modern processes are capable of producing high integrity, near-net-shape castings with excellent surface finishes.
Permanent mold casting is a process used in which permanent molds consists of mold cavities, machined into metal die blocks and appropriate for repetitive use. Advantages This type of casting process is less expensive than die casting or investment casting.
Gravity die casting is an important casting process which has the capability of making complicated, high-integrity components for e.g. the automotive industry. In gravity die castings, the major
MRT Castings is delighted to announce the purchase of a new PFO250 fully automated, die casting cell, from Italian manufacturer Colosio. Read More MRT are exhibiting at Southern Manufacturing & Electronics Exhibition 2019
‘Aluminium Cylinder Head’ castings by Gravity Die Casting process. • Technical Assistance Agreement’ with WP Suspension (subsidiary of KTM). • Joint venture with Magneti Marelli Holdings S.p.A. for manufacture of four-wheeler suspension products in India II. L
Gravity die casting allows for a more precise control over dimensional attributes than sand casting processes are able to. The casting process itself is highly …
This process is also called counter-gravity casting. It is basically the same process as investment casting, It is basically the same process as investment casting, except for the step of …
ABSTRACT :Gravity die casting is used to manufacture the complex metal components where there is a need for high structural integrity. The casting defects that are caused by molten metal include air entrapment, porosity, and shrinkage. But the control of casting defects has been based on the experience of the foundry engineers. This paper describes these defects in casting with the help of
Gravity Die Casting Gravity die casting is a process wherein the liquid metal is poured into metallic moulds without application of any external pressure. The liquid metal enters the cavity by gravity. Gravity die casting (GDC) is different from High Pressure Die Casting (HPDC), where the liquid metal is injected into the metal mould under very high pressures for production of thin walled
the low pressure die casting process. During solidification simulation, the evolution of the solid fraction is calculated and used to predict shrinkage locations. Air back pressure calculations together with appropriate user-defined pressure conditions allow the simulation of vacuum casting processes. High Pressure Die Casting ESI’s QuikCAST allows you to perfectly simulate the piston
Gravity die casting of AC4C aluminum alloy with mechanical vibration (0–120Hz) was conducted. Columnar rod specimens Columnar rod specimens ( 25mm L210mm) were cast to investigate the effect of mechanical vibration on the cooling rate and the dendrite arm spacing of AC4C
Posted on 17th November 2016 Pressure vs Gravity Die Casting. We’ve previously discussed the differences between forging and investment casting, so now we’re turning our attentions to how pressure and gravity die casting differ from each other – and which similarities they have in common.
CMH Articles
SPH based modelling of oxide and oxide film formation in
Die Casting. Gravity die castings are manufactured in aluminium and zinc up to a weight of 25 Kg. High pressure die castings are also manufactured in aluminium and zinc on machines ranging from 250 ton up to 725 ton.
Gravity die casting allows for a more precise control over dimensional attributes than sand casting processes are able to. The casting process itself is highly …
Permanent mold casting is a process used in which permanent molds consists of mold cavities, machined into metal die blocks and appropriate for repetitive use. Advantages This type of casting process is less expensive than die casting or investment casting.
We can produce gravity castings up to 1.5 x 1.2 metres. Shot weights range from 0.2 kilogrammes up to 45 kilogrammes, and we use six different aluminium alloy specifications. We manufacture a diverse range of castings including footplates, valve components, safety-critical suspension assemblies, housings and brackets.
Effective Die Coating for Maximum Value . In gravity diecasting, coatings can be used to present die wear and control metal solidification rate and direction
This paper deals with elimination of defects in aluminium alloy castings produced by gravity die casting process. The main intention of work is to investigate the defects and improve quality of a gravity die cast component using Computer Aided Casting Simulation Software. In this study an industrial gravity casting die is used which was producing defective components. The die and components
Posted on 17th November 2016 Pressure vs Gravity Die Casting. We’ve previously discussed the differences between forging and investment casting, so now we’re turning our attentions to how pressure and gravity die casting differ from each other – and which similarities they have in common.
The die casting die or mold is a closed vessel into which molten metal is injected under high pressure and temperature, then rapidly cooled until the solidified …
the low pressure die casting process. During solidification simulation, the evolution of the solid fraction is calculated and used to predict shrinkage locations. Air back pressure calculations together with appropriate user-defined pressure conditions allow the simulation of vacuum casting processes. High Pressure Die Casting ESI’s QuikCAST allows you to perfectly simulate the piston
Die casting is a process that has been around for several decades. It is a flexible process for producing metal It is a flexible process for producing metal parts by forcing molten metal under pressure into reusable steel molds or dies.
Casting Process Data Sheet. Input Data needed to run the simulation: Sand Casting-Casting Process Data Sheet.pdf. Low Pressure Die Casting-Casting Process Data Sheet.pdf
Gravity Die Casting Gravity die casting is a process wherein the liquid metal is poured into metallic moulds without application of any external pressure. The liquid metal enters the cavity by gravity. Gravity die casting (GDC) is different from High Pressure Die Casting (HPDC), where the liquid metal is injected into the metal mould under very high pressures for production of thin walled
Gravity die casting of AC4C aluminum alloy with mechanical vibration (0–120Hz) was conducted. Columnar rod specimens Columnar rod specimens ( 25mm L210mm) were cast to investigate the effect of mechanical vibration on the cooling rate and the dendrite arm spacing of AC4C
Gravity Die Casting Description. Gravity die casting can also be referred to as chill casting or permanent mould casting. Gravity casting is the process of pouring molten metal into steel or cast iron moulds where there is no force other than gravity.
Gravity die casting allows for a more precise control over dimensional attributes than sand casting processes are able to. The casting process itself is highly …
Aluminum gravity die casting PowerPoint PPT Presentation
A PRACTICAL APPROACH TO ELIMINATE DEFECTS IN GRAVITY DIE
CASTING SIMULATION SUITE esi-group.com
7/04/2017 · In this video of Aluminium Gravity Die Castings where molten Aluminium/Metal is poured into a cast iron gravity die tool. The two hardened tool steel dies has created the cavity which work as
Gravity Die Casting Casting (Metalworking) Alloy
Casting Data Sheet SUTCAST
Linear Casting Tolerances Linear Dimensional Tolerances
Casting Process Data Sheet. Input Data needed to run the simulation: Sand Casting-Casting Process Data Sheet.pdf. Low Pressure Die Casting-Casting Process Data Sheet.pdf
STUDY OF PROCESS PARAMETERS OF GRAVITY DIE CASTING
Gravity die casting of AC4C aluminum alloy with mechanical vibration (0–120Hz) was conducted. Columnar rod specimens Columnar rod specimens ( 25mm L210mm) were cast to investigate the effect of mechanical vibration on the cooling rate and the dendrite arm spacing of AC4C
Pressure vs Gravity Die Casting Dean Group
This paper deals with elimination of defects in aluminium alloy castings produced by gravity die casting process. The main intention of work is to investigate the defects and improve quality of a gravity die cast component using Computer Aided Casting Simulation Software. In this study an industrial gravity casting die is used which was producing defective components. The die and components
CASTING SIMULATION SUITE esi-group.com
Die Design Casting (Metalworking) Foundry
casting processes, such as permanent mold casting process) can be considered a “defect generating process”. Not only an average 5-10% scrap is typically produced, but the type, size and severity of defects are varying. From these considerations, it seems that the potential of high-pressure die-casting and permanent mold casting processes will be completely exploited only when the quality
Gravity Die Casting MRT Specialists in Gravity Die Casting
way to realize the water jacket in the high-pressure-die-casting process with a permanent and retractable steel-core. The weaker structure may lead to higher bore distortions and it
CMH Articles
Gravity die casting allows for a more precise control over dimensional attributes than sand casting processes are able to. The casting process itself is highly …
Carlton Die Casting Gravity and High Pressure Die Casting
Die casting is the process of forcing molten metal, under high pressure, into mold cavities (which are machined into dies). Most die castings are made from non-ferrous metals, specifically zinc, copper, aluminum, magnesium, lead, and tin based alloys, although ferrous metal die castings are possible. The die casting method is especially suited for applications where a large quantity of small
Gravity Die Casting MRT Specialists in Gravity Die Casting
The gravity die casting process is governed by its process parameters so it is required to study its process parameters and its effects. In this paper an effort has been incorporated to study the change in process parameters and their consequent effects on casting defects. Key words:
SPH based modelling of oxide and oxide film formation in
Effective Die Coating for Maximum Value . In gravity diecasting, coatings can be used to present die wear and control metal solidification rate and direction
Carlton Die Casting Gravity and High Pressure Die Casting
Gravity Die Casting MRT Specialists in Gravity Die Casting
MRT Castings is delighted to announce the purchase of a new PFO250 fully automated, die casting cell, from Italian manufacturer Colosio. Read More MRT are exhibiting at Southern Manufacturing & Electronics Exhibition 2019
Gravity Die Casting Carlton Die Cast
Gravity Die Casting Manufacturing Process/machine Castal
This process is also called counter-gravity casting. It is basically the same process as investment casting, It is basically the same process as investment casting, except for the step of …
SPH based modelling of oxide and oxide film formation in
Die Casting Manufacturing Eurobalt Engineering
Effective Die Coating for Maximum Value . In gravity diecasting, coatings can be used to present die wear and control metal solidification rate and direction
A PRACTICAL APPROACH TO ELIMINATE DEFECTS IN GRAVITY DIE
SPH based modelling of oxide and oxide film formation in
The aluminium die casting process is used to create precise, uniform aluminium components. Lupton & Place are some of the most experienced manufacturers in the UK, using the die casting process to ensure a great result for our clients, every time. Learn more about the die casting process on this page or …
Die Design Casting (Metalworking) Foundry
Chapter III: Manufacturing Process & Technology 3.1 Sand casting 3.2 Die casting 3.2.1 Gravity die casting 3.2.2 High pressure die casting 3.2.3 Low pressure die casting 3.2.4 Basic difference between the 3 die casting processes 3.3 Squeeze casting 3.4 Aluminium casting alloys designation 3.4.1 Standards governing aluminium casting alloys 3.4.2 Aluminium casting alloys family and their end …
Gravity Die Casting Manufacturing Process/machine Castal
Posted on 17th November 2016 Pressure vs Gravity Die Casting. We’ve previously discussed the differences between forging and investment casting, so now we’re turning our attentions to how pressure and gravity die casting differ from each other – and which similarities they have in common.
SPH based modelling of oxide and oxide film formation in
‘Aluminium Cylinder Head’ castings by Gravity Die Casting process. • Technical Assistance Agreement’ with WP Suspension (subsidiary of KTM). • Joint venture with Magneti Marelli Holdings S.p.A. for manufacture of four-wheeler suspension products in India II. L
Die Design Casting (Metalworking) Foundry
Aluminum gravity die casting PowerPoint PPT Presentation
Gravity Die Casting Description. Gravity die casting can also be referred to as chill casting or permanent mould casting. Gravity casting is the process of pouring molten metal into steel or cast iron moulds where there is no force other than gravity.
Aluminum gravity die casting PowerPoint PPT Presentation
Die Casting Manufacturing Eurobalt Engineering
The gravity die casting process is suitable for high volume production of non-ferrous alloy castings of Aluminium, Magnesium, Copper and Zinc base alloys and to limited extent for cast iron castings. Castings can be manufactured by operation of dies manually or by automatic devices or through die casting machines depending on the quantum of production. The die materials used are gray cast iron
Gravity Die Casting Manufacturing Process/machine Castal
DIE CASTING AUTOMATION – AN INTEGRATED ENGINEERING
Die Design Casting (Metalworking) Foundry
Gravity Die Casting Description. Gravity die casting can also be referred to as chill casting or permanent mould casting. Gravity casting is the process of pouring molten metal into steel or cast iron moulds where there is no force other than gravity.
Linear Casting Tolerances Linear Dimensional Tolerances
Effects of Mechanical Vibration on Cooling Rate and DAS of
A PRACTICAL APPROACH TO ELIMINATE DEFECTS IN GRAVITY DIE
way to realize the water jacket in the high-pressure-die-casting process with a permanent and retractable steel-core. The weaker structure may lead to higher bore distortions and it
Gravity Die Casting MRT Specialists in Gravity Die Casting
CMH Articles
Effects of Mechanical Vibration on Cooling Rate and DAS of
Die casting is the process of forcing molten metal, under high pressure, into mold cavities (which are machined into dies). Most die castings are made from non-ferrous metals, specifically zinc, copper, aluminum, magnesium, lead, and tin based alloys, although ferrous metal die castings are possible. The die casting method is especially suited for applications where a large quantity of small
Pressure vs Gravity Die Casting Dean Group
Gravity Die Casting Manufacturing Process/machine Castal
Casting Data Sheet SUTCAST
the low pressure die casting process. During solidification simulation, the evolution of the solid fraction is calculated and used to predict shrinkage locations. Air back pressure calculations together with appropriate user-defined pressure conditions allow the simulation of vacuum casting processes. High Pressure Die Casting ESI’s QuikCAST allows you to perfectly simulate the piston
Carlton Die Casting Gravity and High Pressure Die Casting
Gravity Die Casting Manufacturing Process/machine Castal
The gravity die casting process is suitable for high volume production of non-ferrous alloy castings of Aluminium, Magnesium, Copper and Zinc base alloys and to limited extent for cast iron castings. Castings can be manufactured by operation of dies manually or by automatic devices or through die casting machines depending on the quantum of production. The die materials used are gray cast iron
Gravity Die Casting MRT Specialists in Gravity Die Casting
Posted on 17th November 2016 Pressure vs Gravity Die Casting. We’ve previously discussed the differences between forging and investment casting, so now we’re turning our attentions to how pressure and gravity die casting differ from each other – and which similarities they have in common.
CMH Articles
Gravity Die Casting Manufacturing Process/machine Castal
Gravity die casting of AC4C aluminum alloy with mechanical vibration (0–120Hz) was conducted. Columnar rod specimens Columnar rod specimens ( 25mm L210mm) were cast to investigate the effect of mechanical vibration on the cooling rate and the dendrite arm spacing of AC4C
Gravity Die Casting MRT Specialists in Gravity Die Casting
Gravity Die Casting Casting (Metalworking) Alloy
The die casting die or mold is a closed vessel into which molten metal is injected under high pressure and temperature, then rapidly cooled until the solidified …
Gravity Die Casting MRT Specialists in Gravity Die Casting
SPH based modelling of oxide and oxide film formation in
ABSTRACT :Gravity die casting is used to manufacture the complex metal components where there is a need for high structural integrity. The casting defects that are caused by molten metal include air entrapment, porosity, and shrinkage. But the control of casting defects has been based on the experience of the foundry engineers. This paper describes these defects in casting with the help of
Die Casting Manufacturing Eurobalt Engineering
Die casting is the process of forcing molten metal, under high pressure, into mold cavities (which are machined into dies). Most die castings are made from non-ferrous metals, specifically zinc, copper, aluminum, magnesium, lead, and tin based alloys, although ferrous metal die castings are possible. The die casting method is especially suited for applications where a large quantity of small
Gravity Die Casting Carlton Die Cast
Die Casting Manufacturing Eurobalt Engineering
Gravity Die Casting employs cast iron or steel moulds which allow aluminium and zinc castings to be produced more accurately and cheaply than with sand casting, with better surface finish, and better mechanical properties.
SPH based modelling of oxide and oxide film formation in
Die Casting Manufacturing Eurobalt Engineering
Aluminum gravity die casting PowerPoint PPT Presentation
Gravity die casting of AC4C aluminum alloy with mechanical vibration (0–120Hz) was conducted. Columnar rod specimens Columnar rod specimens ( 25mm L210mm) were cast to investigate the effect of mechanical vibration on the cooling rate and the dendrite arm spacing of AC4C
STUDY OF PROCESS PARAMETERS OF GRAVITY DIE CASTING
A PRACTICAL APPROACH TO ELIMINATE DEFECTS IN GRAVITY DIE
Gravity Die Casting Carlton Die Cast
Gravity die casting allows for a more precise control over dimensional attributes than sand casting processes are able to. The casting process itself is highly …
CMH Articles
Gravity Die Castings Die casting products, mainly are cast aluminum alloy and zinc alloy with good dimensions. Lost Foam Castings Lost foam casting products, ductile iron pipe fittings, valves Low Pressure Die Castings Lost pressure die casting products, mainly aluminum alloy casting products.
Linear Casting Tolerances Linear Dimensional Tolerances
Gravity Die Casting Carlton Die Cast
Gravity Die Casting Casting (Metalworking) Alloy
Gravity Die Casting Gravity die casting is a process wherein the liquid metal is poured into metallic moulds without application of any external pressure. The liquid metal enters the cavity by gravity. Gravity die casting (GDC) is different from High Pressure Die Casting (HPDC), where the liquid metal is injected into the metal mould under very high pressures for production of thin walled
Carlton Die Casting Gravity and High Pressure Die Casting
CASTING SIMULATION SUITE esi-group.com
Casting Data Sheet SUTCAST
Gravity Die Casting employs cast iron or steel moulds which allow aluminium and zinc castings to be produced more accurately and cheaply than with sand casting, with better surface finish, and better mechanical properties.
STUDY OF PROCESS PARAMETERS OF GRAVITY DIE CASTING
the low pressure die casting process. During solidification simulation, the evolution of the solid fraction is calculated and used to predict shrinkage locations. Air back pressure calculations together with appropriate user-defined pressure conditions allow the simulation of vacuum casting processes. High Pressure Die Casting ESI’s QuikCAST allows you to perfectly simulate the piston
Die Casting Manufacturing Eurobalt Engineering
CASTING SIMULATION SUITE esi-group.com
Gravity Die Casting Casting (Metalworking) Alloy
casting processes, such as permanent mold casting process) can be considered a “defect generating process”. Not only an average 5-10% scrap is typically produced, but the type, size and severity of defects are varying. From these considerations, it seems that the potential of high-pressure die-casting and permanent mold casting processes will be completely exploited only when the quality
DIE CASTING AUTOMATION – AN INTEGRATED ENGINEERING
ABSTRACT :Gravity die casting is used to manufacture the complex metal components where there is a need for high structural integrity. The casting defects that are caused by molten metal include air entrapment, porosity, and shrinkage. But the control of casting defects has been based on the experience of the foundry engineers. This paper describes these defects in casting with the help of
CASTING SIMULATION SUITE esi-group.com
Gravity Die Casting Carlton Die Cast
Gravity Die Castings Die casting products, mainly are cast aluminum alloy and zinc alloy with good dimensions. Lost Foam Castings Lost foam casting products, ductile iron pipe fittings, valves Low Pressure Die Castings Lost pressure die casting products, mainly aluminum alloy casting products.
Gravity Die Casting Casting (Metalworking) Alloy
Effects of Mechanical Vibration on Cooling Rate and DAS of
ABSTRACT :Gravity die casting is used to manufacture the complex metal components where there is a need for high structural integrity. The casting defects that are caused by molten metal include air entrapment, porosity, and shrinkage. But the control of casting defects has been based on the experience of the foundry engineers. This paper describes these defects in casting with the help of
Effects of Mechanical Vibration on Cooling Rate and DAS of
Aluminum gravity die casting PowerPoint PPT Presentation
The aluminium die casting process is used to create precise, uniform aluminium components. Lupton & Place are some of the most experienced manufacturers in the UK, using the die casting process to ensure a great result for our clients, every time. Learn more about the die casting process on this page or …
Effects of Mechanical Vibration on Cooling Rate and DAS of
DIE CASTING AUTOMATION – AN INTEGRATED ENGINEERING
Die casting is a process that has been around for several decades. It is a flexible process for producing metal It is a flexible process for producing metal parts by forcing molten metal under pressure into reusable steel molds or dies.
Effects of Mechanical Vibration on Cooling Rate and DAS of
Aluminum gravity die casting PowerPoint PPT Presentation
Gravity Die Casting MRT Specialists in Gravity Die Casting
Permanent mold casting is a process used in which permanent molds consists of mold cavities, machined into metal die blocks and appropriate for repetitive use. Advantages This type of casting process is less expensive than die casting or investment casting.
Gravity Die Casting Casting (Metalworking) Alloy
Die Casting. Gravity die castings are manufactured in aluminium and zinc up to a weight of 25 Kg. High pressure die castings are also manufactured in aluminium and zinc on machines ranging from 250 ton up to 725 ton.
A PRACTICAL APPROACH TO ELIMINATE DEFECTS IN GRAVITY DIE
casting processes, such as permanent mold casting process) can be considered a “defect generating process”. Not only an average 5-10% scrap is typically produced, but the type, size and severity of defects are varying. From these considerations, it seems that the potential of high-pressure die-casting and permanent mold casting processes will be completely exploited only when the quality
Pressure vs Gravity Die Casting Dean Group
Aluminum gravity die casting PowerPoint PPT Presentation
SPH based modelling of oxide and oxide film formation in
The gravity die casting process is suitable for high volume production of non-ferrous alloy castings of Aluminium, Magnesium, Copper and Zinc base alloys and to limited extent for cast iron castings. Castings can be manufactured by operation of dies manually or by automatic devices or through die casting machines depending on the quantum of production. The die materials used are gray cast iron
Linear Casting Tolerances Linear Dimensional Tolerances
Pressure vs Gravity Die Casting Dean Group
Gravity Die Casting Casting (Metalworking) Alloy
Permanent mold casting is a process used in which permanent molds consists of mold cavities, machined into metal die blocks and appropriate for repetitive use. Advantages This type of casting process is less expensive than die casting or investment casting.
Gravity Die Casting Casting (Metalworking) Alloy
Gravity Die Casting Description. Gravity die casting can also be referred to as chill casting or permanent mould casting. Gravity casting is the process of pouring molten metal into steel or cast iron moulds where there is no force other than gravity.
Die Design Casting (Metalworking) Foundry
Aluminum gravity die casting PowerPoint PPT Presentation
Pressure vs Gravity Die Casting Dean Group
ABSTRACT :Gravity die casting is used to manufacture the complex metal components where there is a need for high structural integrity. The casting defects that are caused by molten metal include air entrapment, porosity, and shrinkage. But the control of casting defects has been based on the experience of the foundry engineers. This paper describes these defects in casting with the help of
Aluminum gravity die casting PowerPoint PPT Presentation
STUDY OF PROCESS PARAMETERS OF GRAVITY DIE CASTING
Gravity Die Casting Gravity die casting is a process wherein the liquid metal is poured into metallic moulds without application of any external pressure. The liquid metal enters the cavity by gravity. Gravity die casting (GDC) is different from High Pressure Die Casting (HPDC), where the liquid metal is injected into the metal mould under very high pressures for production of thin walled
Die Casting Manufacturing Eurobalt Engineering
Gravity Die Castings Die casting products, mainly are cast aluminum alloy and zinc alloy with good dimensions. Lost Foam Castings Lost foam casting products, ductile iron pipe fittings, valves Low Pressure Die Castings Lost pressure die casting products, mainly aluminum alloy casting products.
CASTING SIMULATION SUITE esi-group.com
The gravity die casting process is suitable for high volume production of non-ferrous alloy castings of Aluminium, Magnesium, Copper and Zinc base alloys and to limited extent for cast iron castings. Castings can be manufactured by operation of dies manually or by automatic devices or through die casting machines depending on the quantum of production. The die materials used are gray cast iron
Pressure vs Gravity Die Casting Dean Group
Effects of Mechanical Vibration on Cooling Rate and DAS of
way to realize the water jacket in the high-pressure-die-casting process with a permanent and retractable steel-core. The weaker structure may lead to higher bore distortions and it
Gravity Die Casting Manufacturing Process/machine Castal
Carlton Die Casting Gravity and High Pressure Die Casting
Die casting is a process that has been around for several decades. It is a flexible process for producing metal It is a flexible process for producing metal parts by forcing molten metal under pressure into reusable steel molds or dies.
Aluminum gravity die casting PowerPoint PPT Presentation
Die Casting Manufacturing Eurobalt Engineering
DIE CASTING AUTOMATION – AN INTEGRATED ENGINEERING
The aluminium die casting process is used to create precise, uniform aluminium components. Lupton & Place are some of the most experienced manufacturers in the UK, using the die casting process to ensure a great result for our clients, every time. Learn more about the die casting process on this page or …
CMH Articles
The gravity die casting process is suitable for high volume production of non-ferrous alloy castings of Aluminium, Magnesium, Copper and Zinc base alloys and to limited extent for cast iron castings. Castings can be manufactured by operation of dies manually or by automatic devices or through die casting machines depending on the quantum of production. The die materials used are gray cast iron
DIE CASTING AUTOMATION – AN INTEGRATED ENGINEERING
Die casting is a metal casting process in which molten metal is forced into a steel mold under high pressure into a mold cavity. The steel molds, known as dies, are fabricated to produce castings with
Pressure vs Gravity Die Casting Dean Group
Gravity Die Casting MRT Specialists in Gravity Die Casting
Linear Casting Tolerances Linear Dimensional Tolerances
Gravity Die Castings Die casting products, mainly are cast aluminum alloy and zinc alloy with good dimensions. Lost Foam Castings Lost foam casting products, ductile iron pipe fittings, valves Low Pressure Die Castings Lost pressure die casting products, mainly aluminum alloy casting products.
Casting Data Sheet SUTCAST
Die Casting Manufacturing Eurobalt Engineering
automatic machines as die-caster operator. 3. Employment opportunities: On successful completion of this course, the candidates shall be gainfully employed in the following industries: 1. Low Pressure die casting Industry. 2. High Pressure Die casting Industry. 3. Gravity Die casting Industry. 4. Further learning pathways: reputed Industries / Organizations. ssful completion of the course
CMH Articles
DIE CASTING AUTOMATION – AN INTEGRATED ENGINEERING
Carlton Die Casting Gravity and High Pressure Die Casting
The gravity die casting process is governed by its process parameters so it is required to study its process parameters and its effects. In this paper an effort has been incorporated to study the change in process parameters and their consequent effects on casting defects. Key words:
Linear Casting Tolerances Linear Dimensional Tolerances
SPH based modelling of oxide and oxide film formation in
Die Design Casting (Metalworking) Foundry
Gravity Die Castings Die casting products, mainly are cast aluminum alloy and zinc alloy with good dimensions. Lost Foam Castings Lost foam casting products, ductile iron pipe fittings, valves Low Pressure Die Castings Lost pressure die casting products, mainly aluminum alloy casting products.
Pressure vs Gravity Die Casting Dean Group
Aluminum gravity die casting PowerPoint PPT Presentation
Gravity Die Casting Casting (Metalworking) Alloy
Gravity die casting is an important casting process which has the capability of making complicated, high-integrity components for e.g. the automotive industry. In gravity die castings, the major
Gravity Die Casting Casting (Metalworking) Alloy
Gravity Die Castings Die casting products, mainly are cast aluminum alloy and zinc alloy with good dimensions. Lost Foam Castings Lost foam casting products, ductile iron pipe fittings, valves Low Pressure Die Castings Lost pressure die casting products, mainly aluminum alloy casting products.
STUDY OF PROCESS PARAMETERS OF GRAVITY DIE CASTING
Gravity Die Casting Carlton Die Cast
Linear Casting Tolerances Linear Dimensional Tolerances
This process is also called counter-gravity casting. It is basically the same process as investment casting, It is basically the same process as investment casting, except for the step of …
CASTING SIMULATION SUITE esi-group.com
CMH Articles
The die casting die or mold is a closed vessel into which molten metal is injected under high pressure and temperature, then rapidly cooled until the solidified …
STUDY OF PROCESS PARAMETERS OF GRAVITY DIE CASTING
Linear Casting Tolerances Linear Dimensional Tolerances
Pressure vs Gravity Die Casting Dean Group
Die Casting. Gravity die castings are manufactured in aluminium and zinc up to a weight of 25 Kg. High pressure die castings are also manufactured in aluminium and zinc on machines ranging from 250 ton up to 725 ton.
Gravity Die Casting Casting (Metalworking) Alloy
DIE CASTING AUTOMATION – AN INTEGRATED ENGINEERING
The die casting process has evolved from the original low-pressure injection method to techniques including high-pressure casting at forces exceeding 4500 pounds per square inch squeeze casting and semi-solid die casting. These modern processes are capable of producing high integrity, near-net-shape castings with excellent surface finishes.
SPH based modelling of oxide and oxide film formation in
Aluminum gravity die casting PowerPoint PPT Presentation
casting processes, such as permanent mold casting process) can be considered a “defect generating process”. Not only an average 5-10% scrap is typically produced, but the type, size and severity of defects are varying. From these considerations, it seems that the potential of high-pressure die-casting and permanent mold casting processes will be completely exploited only when the quality
Gravity Die Casting Manufacturing Process/machine Castal
Die Casting Manufacturing Eurobalt Engineering
CASTING SIMULATION SUITE esi-group.com
automatic machines as die-caster operator. 3. Employment opportunities: On successful completion of this course, the candidates shall be gainfully employed in the following industries: 1. Low Pressure die casting Industry. 2. High Pressure Die casting Industry. 3. Gravity Die casting Industry. 4. Further learning pathways: reputed Industries / Organizations. ssful completion of the course
Effects of Mechanical Vibration on Cooling Rate and DAS of
Gravity Die Casting Manufacturing Process/machine Castal
Gravity die casting allows for a more precise control over dimensional attributes than sand casting processes are able to. The casting process itself is highly …
Gravity Die Casting Casting (Metalworking) Alloy
Effective Die Coating for Maximum Value . In gravity diecasting, coatings can be used to present die wear and control metal solidification rate and direction
Carlton Die Casting Gravity and High Pressure Die Casting
Casting Data Sheet SUTCAST
Die Design Casting (Metalworking) Foundry
Gravity Die Casting employs cast iron or steel moulds which allow aluminium and zinc castings to be produced more accurately and cheaply than with sand casting, with better surface finish, and better mechanical properties.
Casting Data Sheet SUTCAST
Gravity Die Casting Casting (Metalworking) Alloy
DIE CASTING AUTOMATION – AN INTEGRATED ENGINEERING
automatic machines as die-caster operator. 3. Employment opportunities: On successful completion of this course, the candidates shall be gainfully employed in the following industries: 1. Low Pressure die casting Industry. 2. High Pressure Die casting Industry. 3. Gravity Die casting Industry. 4. Further learning pathways: reputed Industries / Organizations. ssful completion of the course
A PRACTICAL APPROACH TO ELIMINATE DEFECTS IN GRAVITY DIE
Linear Casting Tolerances Linear Dimensional Tolerances
This process is also called counter-gravity casting. It is basically the same process as investment casting, It is basically the same process as investment casting, except for the step of …
Gravity Die Casting Casting (Metalworking) Alloy
A PRACTICAL APPROACH TO ELIMINATE DEFECTS IN GRAVITY DIE
DIE CASTING AUTOMATION – AN INTEGRATED ENGINEERING
ABSTRACT :Gravity die casting is used to manufacture the complex metal components where there is a need for high structural integrity. The casting defects that are caused by molten metal include air entrapment, porosity, and shrinkage. But the control of casting defects has been based on the experience of the foundry engineers. This paper describes these defects in casting with the help of
Carlton Die Casting Gravity and High Pressure Die Casting
We can produce gravity castings up to 1.5 x 1.2 metres. Shot weights range from 0.2 kilogrammes up to 45 kilogrammes, and we use six different aluminium alloy specifications. We manufacture a diverse range of castings including footplates, valve components, safety-critical suspension assemblies, housings and brackets.
A PRACTICAL APPROACH TO ELIMINATE DEFECTS IN GRAVITY DIE
CMH Articles
While vacuum die casting of aluminum is widely practiced, there is only one company in North America, Gibbs Die Casting (Henderson, KY), that uses vacuum for die casting magnesium components. Fig. 7 shows the Gibbs vacuum-assisted vertical die casting process [11] .
CASTING SIMULATION SUITE esi-group.com
Aluminum gravity die casting PowerPoint PPT Presentation
Gravity Die Casting Manufacturing Process/machine Castal
The gravity die casting process is suitable for high volume production of non-ferrous alloy castings of Aluminium, Magnesium, Copper and Zinc base alloys and to limited extent for cast iron castings. Castings can be manufactured by operation of dies manually or by automatic devices or through die casting machines depending on the quantum of production. The die materials used are gray cast iron
A PRACTICAL APPROACH TO ELIMINATE DEFECTS IN GRAVITY DIE
Die casting is a metal casting process in which molten metal is forced into a steel mold under high pressure into a mold cavity. The steel molds, known as dies, are fabricated to produce castings with
Gravity Die Casting Carlton Die Cast
way to realize the water jacket in the high-pressure-die-casting process with a permanent and retractable steel-core. The weaker structure may lead to higher bore distortions and it
CMH Articles
MRT Castings is delighted to announce the purchase of a new PFO250 fully automated, die casting cell, from Italian manufacturer Colosio. Read More MRT are exhibiting at Southern Manufacturing & Electronics Exhibition 2019
Carlton Die Casting Gravity and High Pressure Die Casting
Gravity Die Casting Description. Gravity die casting can also be referred to as chill casting or permanent mould casting. Gravity casting is the process of pouring molten metal into steel or cast iron moulds where there is no force other than gravity.
Gravity Die Casting Casting (Metalworking) Alloy
STUDY OF PROCESS PARAMETERS OF GRAVITY DIE CASTING
Gravity die casting allows for a more precise control over dimensional attributes than sand casting processes are able to. The casting process itself is highly …
Gravity Die Casting MRT Specialists in Gravity Die Casting
CMH Articles
SPH based modelling of oxide and oxide film formation in
ABSTRACT :Gravity die casting is used to manufacture the complex metal components where there is a need for high structural integrity. The casting defects that are caused by molten metal include air entrapment, porosity, and shrinkage. But the control of casting defects has been based on the experience of the foundry engineers. This paper describes these defects in casting with the help of
Aluminum gravity die casting PowerPoint PPT Presentation
Casting Process Data Sheet. Input Data needed to run the simulation: Sand Casting-Casting Process Data Sheet.pdf. Low Pressure Die Casting-Casting Process Data Sheet.pdf
SPH based modelling of oxide and oxide film formation in
Effects of Mechanical Vibration on Cooling Rate and DAS of
Gravity Die Castings Die casting products, mainly are cast aluminum alloy and zinc alloy with good dimensions. Lost Foam Castings Lost foam casting products, ductile iron pipe fittings, valves Low Pressure Die Castings Lost pressure die casting products, mainly aluminum alloy casting products.
Gravity Die Casting Carlton Die Cast
Pressure vs Gravity Die Casting Dean Group
the low pressure die casting process. During solidification simulation, the evolution of the solid fraction is calculated and used to predict shrinkage locations. Air back pressure calculations together with appropriate user-defined pressure conditions allow the simulation of vacuum casting processes. High Pressure Die Casting ESI’s QuikCAST allows you to perfectly simulate the piston
A PRACTICAL APPROACH TO ELIMINATE DEFECTS IN GRAVITY DIE
CASTING SIMULATION SUITE esi-group.com
We can produce gravity castings up to 1.5 x 1.2 metres. Shot weights range from 0.2 kilogrammes up to 45 kilogrammes, and we use six different aluminium alloy specifications. We manufacture a diverse range of castings including footplates, valve components, safety-critical suspension assemblies, housings and brackets.
CMH Articles
‘Aluminium Cylinder Head’ castings by Gravity Die Casting process. • Technical Assistance Agreement’ with WP Suspension (subsidiary of KTM). • Joint venture with Magneti Marelli Holdings S.p.A. for manufacture of four-wheeler suspension products in India II. L
STUDY OF PROCESS PARAMETERS OF GRAVITY DIE CASTING
Die Casting Manufacturing Eurobalt Engineering
Die Casting. Gravity die castings are manufactured in aluminium and zinc up to a weight of 25 Kg. High pressure die castings are also manufactured in aluminium and zinc on machines ranging from 250 ton up to 725 ton.
Gravity Die Casting Carlton Die Cast
Gravity Die Casting MRT Specialists in Gravity Die Casting
CMH Articles
The gravity die casting process is suitable for high volume production of non-ferrous alloy castings of Aluminium, Magnesium, Copper and Zinc base alloys and to limited extent for cast iron castings. Castings can be manufactured by operation of dies manually or by automatic devices or through die casting machines depending on the quantum of production. The die materials used are gray cast iron
Carlton Die Casting Gravity and High Pressure Die Casting
Aluminum gravity die casting PowerPoint PPT Presentation
Effective Die Coating for Maximum Value . In gravity diecasting, coatings can be used to present die wear and control metal solidification rate and direction
DIE CASTING AUTOMATION – AN INTEGRATED ENGINEERING
Aluminum gravity die casting PowerPoint PPT Presentation
Die Design Casting (Metalworking) Foundry
The die casting die or mold is a closed vessel into which molten metal is injected under high pressure and temperature, then rapidly cooled until the solidified …
Pressure vs Gravity Die Casting Dean Group
Gravity Die Casting Casting (Metalworking) Alloy
Gravity Die Casting MRT Specialists in Gravity Die Casting
Gravity Die Castings Die casting products, mainly are cast aluminum alloy and zinc alloy with good dimensions. Lost Foam Castings Lost foam casting products, ductile iron pipe fittings, valves Low Pressure Die Castings Lost pressure die casting products, mainly aluminum alloy casting products.
Gravity Die Casting Casting (Metalworking) Alloy
CMH Articles
Gravity Die Casting employs cast iron or steel moulds which allow aluminium and zinc castings to be produced more accurately and cheaply than with sand casting, with better surface finish, and better mechanical properties.
Gravity Die Casting Carlton Die Cast
STUDY OF PROCESS PARAMETERS OF GRAVITY DIE CASTING
Die Design Casting (Metalworking) Foundry
The gravity die casting process is governed by its process parameters so it is required to study its process parameters and its effects. In this paper an effort has been incorporated to study the change in process parameters and their consequent effects on casting defects. Key words:
Gravity Die Casting MRT Specialists in Gravity Die Casting
DIE CASTING AUTOMATION – AN INTEGRATED ENGINEERING
Linear Casting Tolerances Linear Dimensional Tolerances
The die casting die or mold is a closed vessel into which molten metal is injected under high pressure and temperature, then rapidly cooled until the solidified …
DIE CASTING AUTOMATION – AN INTEGRATED ENGINEERING
Gravity Die Casting Manufacturing Process/machine Castal
Die Casting. Gravity die castings are manufactured in aluminium and zinc up to a weight of 25 Kg. High pressure die castings are also manufactured in aluminium and zinc on machines ranging from 250 ton up to 725 ton.
Gravity Die Casting Casting (Metalworking) Alloy
Pressure vs Gravity Die Casting Dean Group
Casting Data Sheet SUTCAST
casting processes, such as permanent mold casting process) can be considered a “defect generating process”. Not only an average 5-10% scrap is typically produced, but the type, size and severity of defects are varying. From these considerations, it seems that the potential of high-pressure die-casting and permanent mold casting processes will be completely exploited only when the quality
Gravity Die Casting Manufacturing Process/machine Castal
Casting Data Sheet SUTCAST
STUDY OF PROCESS PARAMETERS OF GRAVITY DIE CASTING
Permanent mold casting is a process used in which permanent molds consists of mold cavities, machined into metal die blocks and appropriate for repetitive use. Advantages This type of casting process is less expensive than die casting or investment casting.
Die Design Casting (Metalworking) Foundry
Pressure vs Gravity Die Casting Dean Group
Gravity Die Casting Description. Gravity die casting can also be referred to as chill casting or permanent mould casting. Gravity casting is the process of pouring molten metal into steel or cast iron moulds where there is no force other than gravity.
CASTING SIMULATION SUITE esi-group.com